Progressive Cavity Pump Systems: When Precision and Repeatability are Vital
As recently as half a decade ago, operators of manual and automated dispensing lines had little ability to achieve highly accurate, consistent applications of adhesives, epoxies and other fluids, especially when desiring small depositions, working with viscous materials, and/or when attaining the fastest possible throughput speed was a priority.To get more news about
Progressive cavity pump part, you can visit brysonpump.com official website.
For example, jetting valves—perhaps the gold standard for high speed, micro-deposit application capabilities—can be unsatisfactorily turbulent in their accuracy. Time/pressure dispensers and auger valves can deliver accuracy down to ±10% and ±5% respectively, but have a variance that might be unacceptable for many operators, with deposit size impacted throughout the process by temperature-driven changes in material viscosity, as well as fluctuations in air pressure created by the changing fluid level in the syringe barrel. And, the original volumetric or positive displacement pumps such as piston and gear pumps, while delivering the ability to get closer to the “holy grail” accuracy level of ±1%, are often more limited in bead size range and can manifest speed deficits due to their need to fill and refill between depositions.
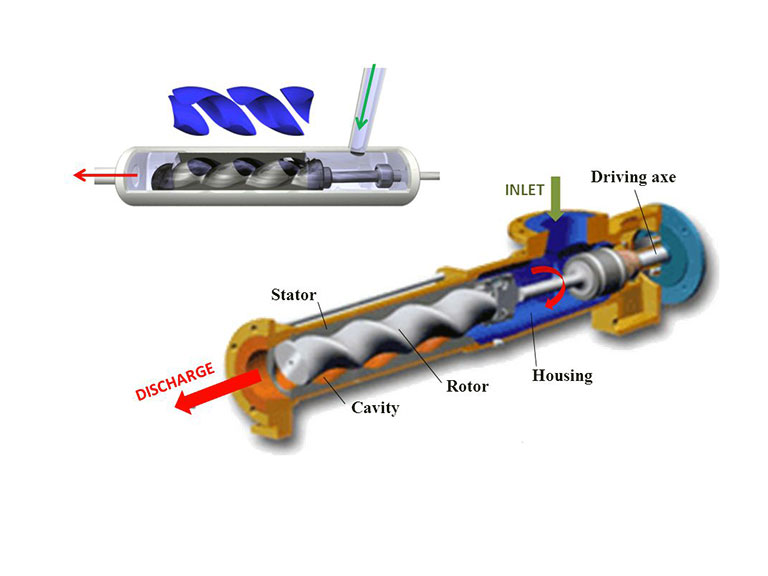
For many organizations, of course, these limitations—and the mandatory balancing act among variables—were, and continue to be acceptable, with the necessary compromises falling within their business operating goals. However, for an increasing number of companies in numerous highly competitive industries, where attaining the optimum levels of accuracy, consistency and speed can translate quickly into a stronger market position and greater profitability, the search for a superior adhesive and epoxy dispensing option continued.
Adapting progressive cavity pump technology to new applications
Looking to heavy industry such as oil drilling and cement processing, innovative dispensing equipment manufacturers noted the potential of progressive cavity pump technology, a unique type of positive displacement pump technology long proven in use in a number of critical applications, such as continually moving large volumes of heavy oils and slurries from deep underground. With the technology now successfully miniaturized and adapted to a table top or assembly line appropriate footprint, progressive cavity pumps offer a number of advantages over incumbent dispensing methods.
For example, unlike other types of epoxy and adhesive dispensing solutions, including other types of positive displacement/volumetric pumps and time/pressure valves, a progressive cavity pump is both a sealed system and a continuous flow operation. Progressive cavity pumps have proven their ability to dispense microbeads as small as a microliter, using a wide range of materials with viscosities ranging from 1 to 300,000 centipoise or more. And, since internal material flow is continuous, rather than relying upon a filling/refilling approach, throughput speeds are consistently high.
Most dramatically, however, progressive cavity pumps can deliver volumetric dispensing accuracy up to ±1%, and do so consistently, unimpacted by ambient temperatures and pressures that plague unsealed pumps that are exposed to environmental conditions, or by variations due to changing material volume levels during operation.
How it works
The essence of a progressive cavity pump is that it operates by use of a continuous rotor/stator configuration, rather than by having material being ejected from filling/refilling chambers at fixed, separate intervals. In this technology, the feed fluid—from plain water all the way to high viscosity greases or solders—is held in a reservoir under positive pressure supplied by an air line which forces it out of the barrel into the fluid feed path and then to the rotor/stator chamber assembly.
The metal, single-helix rotor continuously turns inside a flexible rubber stator molded with a twin helix shaped aperture, forming a constantly shifting series of tightly sealed cavities which move a precise, consistent volume of material steadily and continually toward the pump outlet. From there, fluid is driven to the dispense tip outlet with a flow rate dependent upon the rotor rotation in the feed direction, precisely controlled by the desired specifications dialed into a proprietary controller paired with the system. Of note, with this technology the flow rate is adjustable at any time by changing the motor speed on the controller, as opposed to having to stop operation to adjust the pump itself, further enhancing speed and flexibility. The fluid is dispensed from the tip by means of a voltage signal applied to the motor, and shearing is achieved by reverse Z-motion/tip retraction.
You need to be a member of On Feet Nation to add comments!
Join On Feet Nation